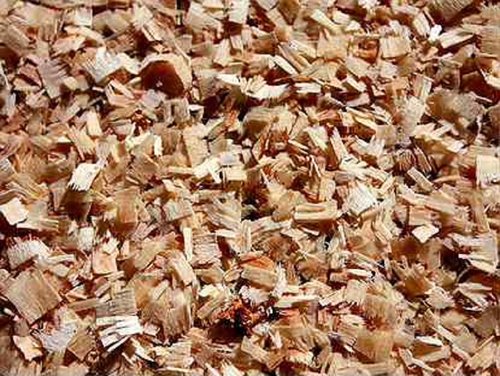
Технологическая цепочка зависит от исходного сырья (это могут быть опилки, листья, лузга) и формы брикета. Однако у предприятий обычно есть оборудование для выполнения всех этапов.
Производство брикетов из опилок: измельчение и сушка
Эти процедуры допустимо менять местами или исключить, если речь идет о небольшом производстве, например, работе домашней установки. Но все же советуем не отказываться от них, даже при незначительных объемах. Это влияет на качество готового товара.
Сушка, которую, как правило, проводят в печах туннельного типа, улучшает прессование. А предварительное измельчение в дробилках упрощает пропуск материала через конвейер.
Прессование
Подготовленный продукт загружается в пресс для брикетов из опилок, где под давлением нагревается до 240-320 градусов и спекается. Связующим компонентом выступает выделяемый при этом лигнин — органический полимер, который содержится в растительных клетках. Есть модели аппаратов, где сырье нагревают ТЭНы при подаче на шнек.
При работе с вторсырьем можно добавлять другие склеивающие компоненты, но делать это нужно заранее. Не обойтись без специального бака-смесителя, в котором все составляющие дойдут до однородного состояния.
Чтобы оборудование служило долго, нужно избегать перегрузок, соблюдать требования расхода и контролировать однородность компонентов.
Резка и упаковка
Полученные топливные брикеты из опилок обрезают и отправляют на паллеты для охлаждения. Затем их нужно упаковать, чтобы исключить поглощение влаги.
Виды брикетов
- RUF. Выглядит как кирпич (150×90×60 мм). Изготавливают на гидравлическом прессе. Упаковка в водозащитную обязательна.
- Pini Kay. Выпускают на шнековом прессе. Брусок длиной 25-40 см, выходит сразу покрытый спекшейся пленкой. Она частично защищает его влажности. Дополнительно возможна фасовка в мешки из полипропиленовой ткани.
- Nestro. Бруски цилиндрической формы диаметром 90 мм, длиной — 50-100 мм. Получают на гидравлическом прессе.